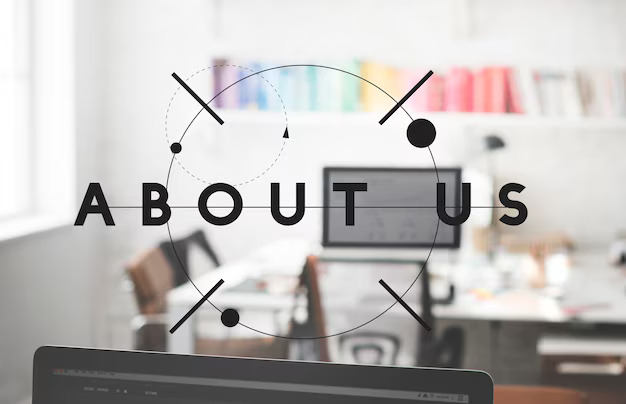
MK FASTENERS
-
There is an MK Fastener in every movement. Your Specification - Our Execution
We manufacture a range of parts for various automotive applications and are used in various safety and critical applications such as, engine systems, brake assembly, fuel systems, spark plug housings, seating mechanisms, seat belts, airbag deployment systems, window regulators, clutch assembly, transmission systems, suspension systems, window regulators, car interior mountings, lighting systems, door hinges, hood & boot latches, starters and alternators, to name a few.
We make Fasteners of various shapes, profiles, dimensions and accuracies, primarily from Mild Steel, Medium Carbon Steel, Brass, Copper, Aluminum Alloy, Nickel Alloy and Stainless Steel as per customer specifications. This can include various, bolts, screws, studs, rivets, pins, shafts, housings, nuts, spacers, and special automotive components.-Manufacturing
World Class Infrastructure for a Global Edge - A Perfect Blend of Mind and Machinery
Cold Forging
The Cold Forging or Cold Forming process is a key manufacturing process at MK Fasteners, and many decades of expertise and effort have been contributed to making us an innovator in this technology and process. The facilities for Cold Forging are vast and range from, single-station headers to multi-station part formers, with input wire sizes ranging from 2 millimeters to 20 millimeters. The facility boasts the best Cold Forging machinery from brands such as Asahi Okuma, Asahi Sunac, Nakashimada, Itami, Carlo Salvi, National Machinery, Sacma, Nedschroef, Hilgeland, Jern Yao, Sakamura, Omega, and Sima, to name a few. These machines are carefully selected to provide high speed and precision, such that even the most difficult and critical components are manufactured with relative ease.
Thread Rolling
The Thread Rolling division works in conjunction with the Cold Forging divisions to provide quick process flow for parts that require this process. At MK Fasteners, the Thread Rolling division has a wide variety of machines that can provide a variety of simple and complex threading, knurling and grooving processes.
Part Forming
The Part Forming facility is a recent implementation to provide solutions for very complex, highly critical, and high accuracy parts. (Bolt parts, Nut parts, etc.) At MK Fasteners, we have a part formers with input wire sizes ranging from 11 millimeters to 20 millimeters.
Nut Forming & Tapping
MK Fasteners has a state of the art Nut Forming & Tapping facility that can produce bushes, simple and complex nuts, which range from sizes M3 to M6 for automotive and non-automotive applications.
Heat Treatment - Under Implementation (2015)
Continuous Mesh Belt Heat Treatment Furnace to be installed and operational by Q4 2015
Surface Treatment (Plating and Coating) - Under Implementation (2016)
Highly Advanced Surface Treatment facility to be installed and operational by Q1 2016-Engineering
Your Specification - Our Execution
Our in-house Design & Development Team consists of highly-skilled personnel capable of producing advanced models with the use of modern engineering concepts and tools to provide our customers with the most relevant and accurate products. Meticulous planning during the concept and prototyping stages allows for us to support our customers with components and fasteners at ideal costs, streamlined production processes and assured quality standards.
At MK Fasteners, the pursuit for enhancing and upgrading engineering technology is a constant function, where leveraging appropriate technologies, upgrading machinery, and employing skills sets beyond our existing capabilities is integral to meet our customers’ changing demands. The Research and Development at our company maintains its focus and efforts to constantly update process control and innovate efficient tooling.
Tool Design and Development for complex and highly critical components are regularly outsourced to the most reputed Cold Forming Tool manufacturing companies from Japan, Germany and Taiwan, to garner their technical expertise for our customer’s benefit.Quality
Inspired by Customers, Driven by Attitude - Quality is the Difference
“We are committed to comply with the most exacting customer needs and provide satisfaction through prompt supply of right quality products, at the right time, in the right quantity and at the right price”
Our company’s Quality Policy sustains our attitude and approach towards Quality Control and Quality Management Systems. We have had the privilege of being presented various awards and accolades from our customers in the automotive and aerospace industries, recognizing our overall performance, quality and on-time delivery. Vigilant efforts are made daily to ensure the standards of performance that has been set, and our aim is to achieve and continue the supply of ‘Zero Defect’ parts to maintain the status of Direct Online Supplier and Green Channel Supplier amongst some of our customers.
To provide this level of quality, we employ a judicious selection of suppliers to ensure in-process quality assurance and maintain final inspection with the use of Optical Sorting Machines (HD Camera based) and Eddy Current Machines to ensure delivery of 100% defect-free parts and components.
Happy Clients and lots more year ahead will be added.
Projects of unsurpassed products and services to the clients.
Support To embrace new technologies and methods.
Hard Workers provide high quality service to customers.